Materials, Manufacturing, Design & Beyond
Research Experience
Postdoctoral Research Associate in Idaho National Laboratory
Project Title: Diffusion Welding of Compact Heat Exchangers for Nuclear Applications (US Department of Energy)
Achievement: Lead the project and fabricated structures that have enhanced joint quality and mechanical properties. This project has wide applications in the solar and nuclear industries. One US patent application is being filed, research highlights will be presented at the ASME PVP Conference in 2022 and published in prestigious journals
Post-doctoral Fellow in Laser-Aided Manufacturing Processes Lab in the Department of Mechanical and Aerospace Engineering, Missouri University of Science and Technology
Project I: Development of Functionally Graded Materials for Thermal Efficiency Enhancement using Directed Energy Deposition (supported by US NSF)
Aimed to fabricate copper-stainless steel functionally graded materials to manufacture structures with enhanced thermal efficiency for power generation and heat exchangers applications
Overcame challenges in fabricating copper-stainless steel structures including cracking, porosity, poor bonding, and high residual stress at the joint
A ~370% increase in thermal diffusivity of the structure demonstrated the high thermal efficiency of the novel structures. Published four high-impact journal papers
Project II: Smart Structures Design and Fabrication using Additive Manufacturing
Aimed to embed optical sensors in Ti6Al4V components for real-time health monitoring
Designed processes to embed optical sensors using directed energy deposition
Characterized the material, mechanical, and optical properties of the smart parts
Project III: Development of High-Throughput Automated Tensile Testing System (supported by US DOE)
Designed and manufactured a high-throughput automated tensile machine for testing irradiated materials in nuclear hot-cell. Significantly reduced mechanical testing time and cost




Advanced Characterization Intern at the Idaho National Laboratory
Fabricated SS316L - Inconel 625 functionally graded materials using directed energy deposition to enhance radiation tolerance for advanced nuclear reactors
Conducted in-situ synchrotron diffraction to study the microstructure and mechanical behavior of the SS316L – Inconel 625 functionally graded materials
Fabricated SS316L fuel cladding and demonstrated the benefits of printed SS316L for nuclear reactors
Conducted in-situ and ex-situ synchrotron diffraction on AM SS316L under thermal annealing
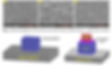
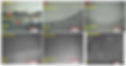







Ph.D. Researcher in Laser-Aided Manufacturing Processes Lab in the Department of Mechanical and Aerospace Engineering, Missouri University of Science and Technology
Project I: Advanced Functionally Graded Materials Design and Fabrication via Directed Energy Deposition (supported by Toyota Motor)
Aimed to fabricate copper-tool steel functionally graded materials for design and manufacturing novel dies/molds for shaping automotive and aerospace components to enhance manufacturing efficiency
Addressed critical issues in fabricating copper-tool steel functionally graded materials via directed energy deposition and achieved novel structures with excellent mechanical properties and 2x thermal efficiency
Investigated residual stress distribution using thermo-mechanical modeling and simulation
Published three high-impact papers and demonstrated benefits for the automotive and aerospace industries






Project II: Automated Die Repair Framework using Hybrid Manufacturing (supported NSF & Toyota)
Aimed to develop automated component repair and remanufacturing process to benefit automotive and aerospace industries for cost reduction as well as time and energy savings
Developed and demonstrated automated component repair process by designing CAD/CAM software
Developed Python program to integrate robot-assisted 3D scanning, STL modeling manipulation, model alignment, damage detection, repair volume reconstruction, tool path generation, additive, and subtractive manufacturing experiments for component repair and remanufacturing
Published six journal papers based on this research. Conducted two international conference presentations, including Best-Paper Award at the International Solid Freeform Fabrication Symposium. The developed program has been delivered to Toyota





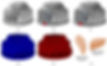
Project III: Development of Repair Process for Ti-6Al-4V Aircraft Parts (supported by Boeing Aerospace)
-
Aimed to develop an automated repair process for repairing critical and expansive aircraft components
-
Built a stereo vision-based automated repair process to automatically locate defects on aircraft parts and reconstruct the repair volume and generate the repair tool path
-
Demonstrated success of the repair process by additive + subtractive manufacturing and mechanical testing with the publication of three papers, evidencing significant values for aerospace industries​



Project IV: Development of a Wire-fed Metal AM System (supported by GKN Aerospace)
-
Developed wire-fed additive manufacturing system to print titanium components for aerospace applications to significantly increase printing speed and reduce material waste
-
Determined key techniques and processing window for wire deposition of titanium with 6X faster than powder-fed and near 100% material utilization to demonstrate the benefits of wire-fed AM process
-
Mentored and trained three undergraduate students during this project
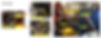

Project V: Process Parameters Optimization in Repairing Die/Mold using AM (supported by Toyota Motor)
-
Determined critical process parameters in depositing Co-based (Wallex 40 and Wallex 50) and Ni-based (Inconel 625, Colmonoy 88L) alloys on tool steel for component repair
-
Demonstrated superior properties of the repaired parts better than new parts through microstructure characterization and mechanical testing​
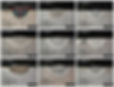

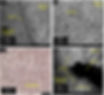
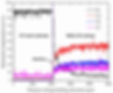


Project VI: Laser Cladding of Ni- and Co-based Alloys on Fuel Injector Components (supported by Cummins)
-
Aimed to clad hard surfacing alloys on engine fuel injectors to enhance wear and corrosion resistance
-
Successfully coated Ni-based (Inconel 625, Colmonoy 88L) and Co-based (Wallex 40 & 50) alloys on fuel injectors using directed energy deposition
-
Performed design of experiments and obtained optimized process parameters to guarantee excellent coating quality. Solved cracking and deformation in cladding hard surfacing alloys on fuel injectors
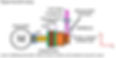



Project VII: Development of Pre-Repair Processing Strategies for Laser-aided Metallic Component Remanufacturing (supported by Toyota)
-
Developed methodologies and Python programs for pre-repair machining of directly non-repairable metallic components to guarantee they are ready for repair through direct metal laser melting process. Pre-machined defects including indentations, surface erosion/corrosion/wear, cracking and deformation
-
Analyzed properties of worn parts and conducted pre-repair heat-treatment on worn components to restore nominal mechanical properties to ensure the high quality after repair
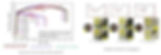

Graduate Researcher, Hubei Key Laboratory of Advanced Technology for Automotive Components, Department of Automotive Engineering, Wuhan University of Technology
Analytical Design Method and Kinematic Analysis in Cold Orbital Forging Process
-
Proposed mathematical model for designing upper tool for cold orbital forging of automotive parts
-
Developed kinematic mathematical model of the upper tool in cold rotary forging process
-
Simulated material deformation in cold orbital forging of automotive gears using the proposed model
-
Investigated the influence of path planning on metal flow and strain/stress distribution in cold rotary forging of automotive components




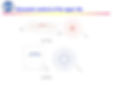
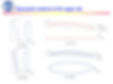


Projects - BS
1. Designed three projects for two China National 3D Innovative Design Competitions and one Shandong Province College Students Mechanical and Electrical Products Innovation Design Competition, Aug. 2010 - Oct. 2012
-
Led and designed a flyable vehicle and adaptive hybrid truck for 4th and 5th China National 3D Innovative Design Competition (Won Grand Prize and First Prize), and a small vehicle kinematic energy recycling system (Won First Prize) for 2011 Shandong Province College Students Mechanical and Electrical Products Innovation Design Competition
-
Modeled and assembled projects in SolidWorks, Creo and NX. Simulated motion of the systems in SolidWorks. FEA Simulated in SolidWorks. Manufactured parts for the small vehicle kinematic energy recycling system using CNC and EDM

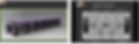
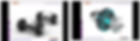

2. Bachelor of Science Graduation Project, Jan. 2013 - Jun. 2013
-
Designed a Two-Speed Automatic Transmission for Low-Speed Electric Vehicle
-
Designed transmission gear ratios, structure and hydraulic circuit of the transmission
-
Validated strength of each part based on mathematical calculation and modeled each part, assembled and motion simulated in SolidWorks

